Premier Mechanical Blog
Actionable tips, community conversations, and inspiration.
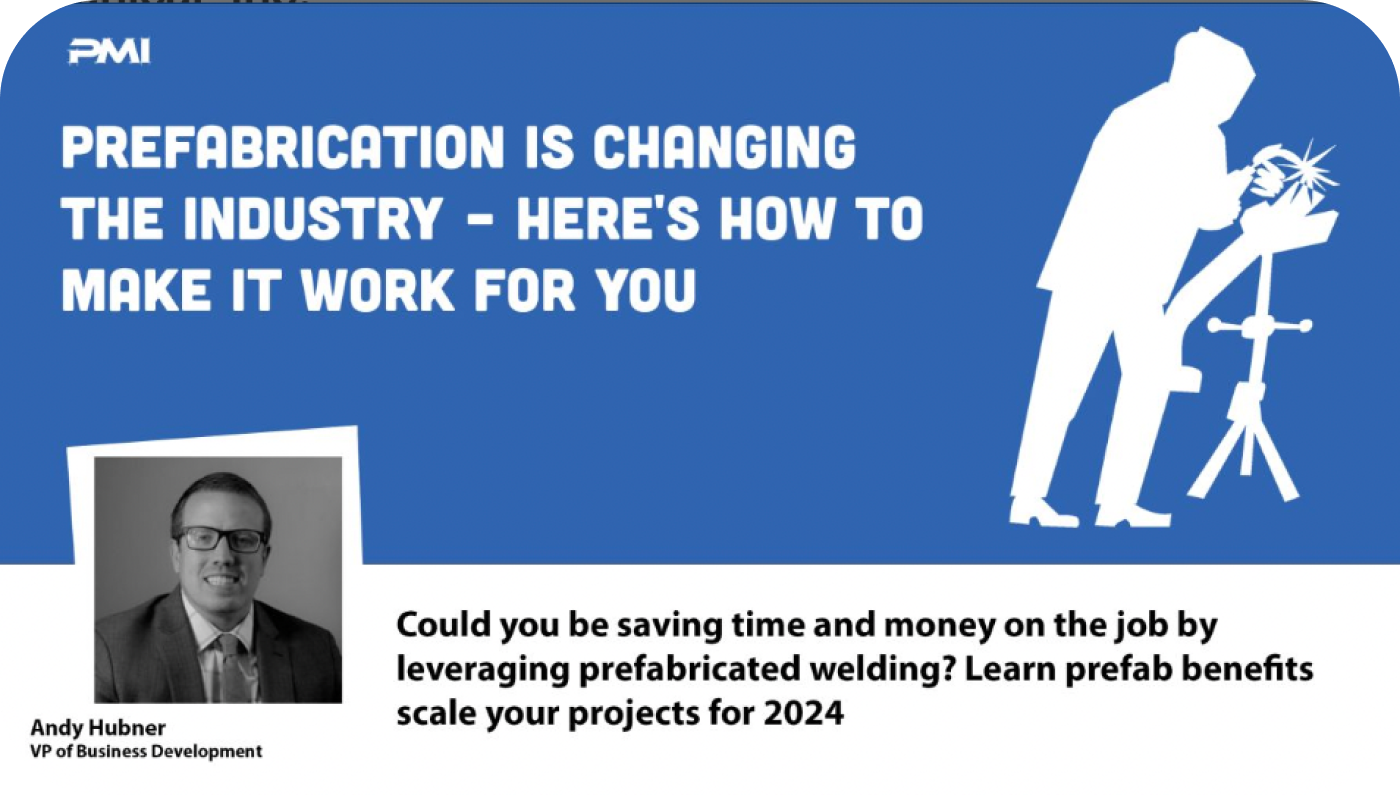
The goal of every mechanical is to complete ethe project on time, with quality workmanship and below budget for the general contractor. Achieving that scale can be challenging and requires a commitment to its success from estimating to design to the crew installing the material in the field. When leveraged correctly, prefabrication welding catalyzes a team's ability to scale projects and complete jobs efficiently with with quality and precision. Many mechanical contractors limit prefabrication to welding. Currently, field welding is the industry standard as that was the default option prior to fully developed virtual models. With the advent of these models, prefabrication has become the gold standard. As a mechanical it is important to incorporate these capabilities into your projects. How Can You Decrease Field Welds and Costs? Companies that use prefabrication welding for their projects not only decrease the number of field welds correlating to a faster installation but also decrease errors in the field. For PMI, welding is an element of the fabrication process. It forces our team to build projects virtually, which uncovers issues at a much earlier stage than with site fabrication. Eliminating these issues decreases overall construction time and reduces costs due to errors and misapplication of equipment. When leveraging a team like PMI creating skids with fully assembled equipment is the byproduct of these virtual models and a fully developed fabrication shop. The extent to which a contractor can adopt these models varies depending on the project. A small amount of fabrication welding can help your team avoid bottlenecks in the production process. In cases where the project allows more time for planning paired with a short construction window, like a summer school project or an equipment replacement project, a fully developed BIM model provides more options and may be a stronger alternative to classical field welding. The hesitancy to embrace prefabricated piping in HVAC me chanical construction does not stem from a lack of potential benefit but rather from and unwillingness to deviate from existing processes. Prefabrication is available through fabrication shops and can reduce your man-power peaks. Currently, industries out there are using this method to fabricate things like aircraft carriers, and soon enough, the fabrication of entire nuclear power plants. The underutilization of prefabricated welding is surprising given its powerful capabilities. Understanding the advantages of this approach can save your team time and some major headaches on your next project.